During our four-day visit to Automate 2024, we were treated to demonstrations from a host of innovators in machine vision and image processing. One of these was Musashi AI, who provided us a rundown of their array of solutions.
Unlike in previous shows where Musashi AI have shown collaborative robots with end-of-arm optics inspecting different part types, this time they presented a full automation system for a specific part.
Frederick Reinink, Business Development at Musashi AI North America, explained this to us:
“This is made up of two stages; there’s an overhead camera system where the robot picks up parts and presents it back to the first stage for checks. Then it goes to the second stage for some additional checks on the body service of the part. In total, the full part is being inspected. The value of this system is that manufacturers of this part have an alternative to manual inspection. A cell like this could do the work of three to six manual inspectors.”
This solution has received plenty of interest from the automotive and medical sectors, but any industry which requires various elements of inspection can benefit from using Musashi AI’s products. The company predominantly focuses on manufacturers that have mid-to-high level volumes, where they can create this solution for them. They make software as well, being a turnkey software provider. Musashi AI works with customers to understand the requirements and then builds the software accordingly.
Frederick also explained the process of building this system:
“We have the design and the building material. We can hand that over to the preferred integrator of the manufacturer, as they know you and your standards. This is what the system needs to have, and then they can assist with that integration.”
Post inspection, all of the data is entered into a database, which can be accessed through a web application. This allows users to look at the production throughput, yield rate, and presence of defects. If there are any defects, users can filter based on the type of defect and its location on the part.
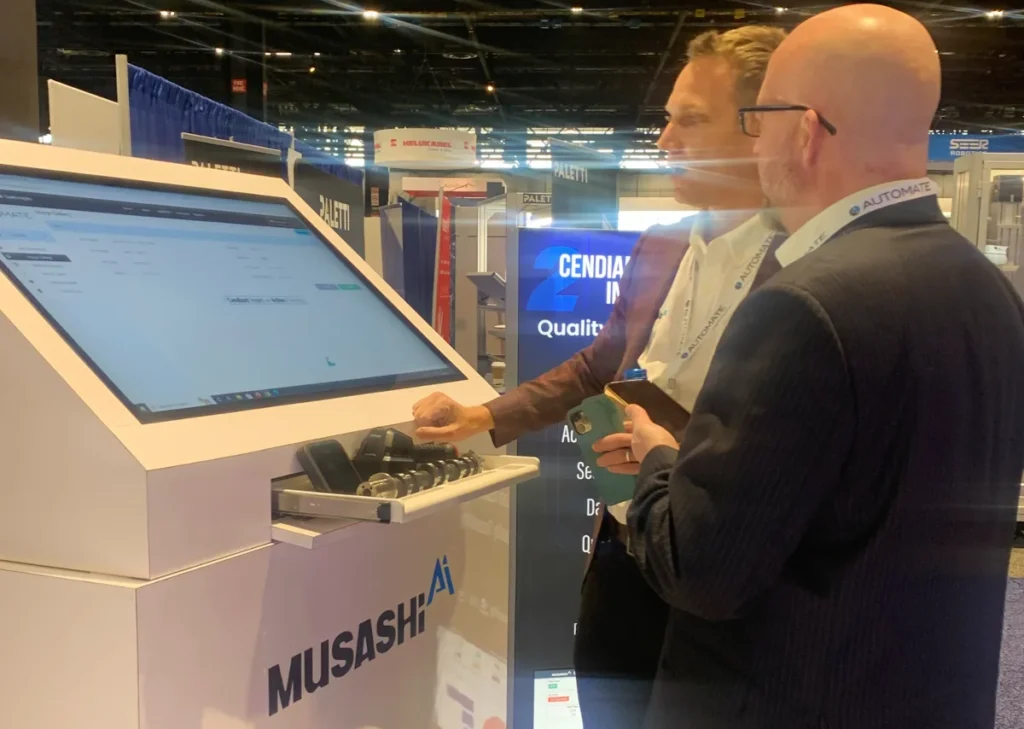
Frederick revealed that traceability is another use-case for this application, saying:
“In many sectors including the automotive space, a lot of the parts have a unique identifier. If a customer reports that a part is faulty, you can go into the database of inspected parts and cross-reference this.”