The Impact of Generative AI – Mark Williams, European Editor at Large
35 years ago in the early years of the machine vision industry, real-time machine vision systems required large racks of dedicated hardware, often exceeding $20,000 in cost. When combined with the need for low-level programming skills and the general lack of machine vision expertise, the true implementation cost of a vision system could reach up to ten times the hardware cost, nearing $200,000. The problem in hand had to be very substantial to justify these costs so the adoption of vision systems was limited to applications such as nuclear and other hostile high value applications. However, the machine vision industry has since benefited from advancements in electronics, largely driven by Moore’s Law, which states that the number of transistors on a silicon chip doubles approximately every two years. As a result, cameras have become more affordable while their resolution and capture speed have significantly improved along with exponential improvements in processing power to deal with the extra data.

European Editor @ Large
The interface between cameras and processors has also evolved from expensive custom cable solutions to standardized connections. The introduction of Camera Link as the first machine vision standard marked a the first major step in simplifying the implementation of a vision system followed by leveraging widely used computing interfaces such as Gigabit Ethernet and later USB 2 and 3. Increasing computational power in PCs eliminated the necessity for custom processing hardware, enabling the development of more advanced and robust algorithms. Additionally, user-friendly, point-and-click development tools simplified and accelerated the creation of vision systems.
The emergence of smart cameras further streamlined the deployment of basic vision systems by integrating the camera, processor, software, and even fundamental lensing and lighting. Initially, smart cameras had to rely on lower-performance processors and slower, lower-resolution sensors due to size and heat dissipation constraints. However, advancements in embedded processors, driven by the mobile phone industry, have significantly enhanced their capabilities, making them suitable for a broader range of applications.
Despite these technological advancements, high-end machine vision market remains buoyant. Discussions with one of the largest machine vision hardware manufacturers in the past year revealed that more image acquisition cards are sold today than before the advent of smart cameras or standard PC interfaces such as USB and Ethernet. This trend can be attributed to the increasing demand for high-resolution, high-frame-rate cameras that surpass the capabilities of smart cameras and standard PC interfaces. These advanced sensors facilitate complex applications, necessitating hardware systems that still cost over $10,000. Additionally, PC-based vision systems remain preferable for multi-camera setups, as they provide more efficient communication and processing than multiple interconnected smart cameras.
Innovations such as GPUs designed for gaming have enabled deep learning, making it possible to solve previously infeasible tasks with minimal training and until very recently required a powerful PC. The adoption of 3D and hyperspectral cameras has further expanded applications, including bin picking and detecting invisible contaminants in food. However, implementing such systems remains complex and requires expert knowledge and a low of computing resources. The total cost of deploying a validated and robust vision system still significantly exceeds the hardware expenses due to the expertise needed for specification, design, implementation, and validation.
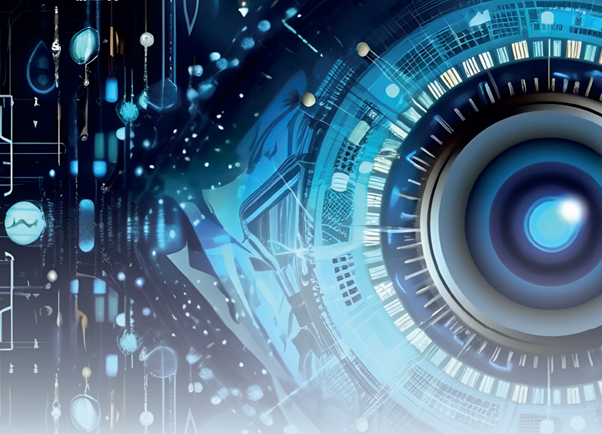
At the entry level, basic smart cameras are available for under $1,000 and has allowed for vision systems to address a far wider number of applications. A well-chosen smart camera may have processing power comparable to a five-year-old PC, but the overall cost will still be many times the hardware cost. The proper specification of components, testing of good and defective samples, and validation under all conditions remain critical. In many cases, vision systems are found deactivated in factories due to improper specification and implementation.
This often results from limited understanding on both the customer and supplier sides especially where the products are supplied by general automation suppliers rather than vision specialists. To aid best practice vision system design the VDMA trade association launched the VDI/VDE/VDMA 2632 standard, a framework to ensure both customer and integrator supplier correctly understand the roles and requirements of a successful implementation. The use of an expert is critical in the deployment and remains the most significant component in the total cost of implementation.
Reducing implementation costs remains a key challenge, and significant progress is anticipated in the coming years. A few years ago, a promising approach called Virtual Inspection Planning was introduced by Petra Gospodnetić from the Fraunhofer Institute at the annual European Machine Vision Association conference. This concept aims to evaluate machine vision system designs before physically building them. Digital twins have been employed for over a decade in the design and modelling of high-cost projects, particularly in robotics, where production lines are simulated before implementation. While initial scepticism surrounded the feasibility of modelling vision systems instead of constructing them directly, recent advancements have made this approach more practical.
At Vision 2024 in October, the startup Medasby showcased a platform that takes virtual evaluation a step further. Their technology integrates digital twins of various machine vision manufacturers and generates synthetic images of defects on products, making it increasingly feasible to validate machine vision system designs without hardware. This innovation is expected to gain traction, particularly in complex applications, where it could significantly reduce planning costs, the company suggests savings up to 35% of the implementation time.
Looking ahead, the impact of generative AI on machine vision system design was a key topic during a panel discussion at Vision 2024. Panellists expressed mixed opinions, citing concerns over intellectual property protection and liability if an AI-generated vision system design proved faulty. However, generative AI tools have the potential to streamline the design phase, increasing efficiency for vision engineers and thus reduce design and validation costs.
The company that successfully harnesses these tools has the potential to introduce a transformative solution, drastically reducing implementation time and costs—probably more than any future hardware cost reductions.
While Generative AI will not replace vision experts in the mid-term at least, it is expected to automate the design process significantly making the vision experts significantly more efficient. Combined with digital twins and synthetic generation of defect images, Generative AI advancements will likely drive the greatest reduction in total vision system costs due to the improved efficiency in the coming years, making the adoption of machine viable in even more applications. The evolution of this technology in our industry will be fascinating to observe.